CNC machining technologies revolutionize manufacturing by automating processes through computer-controlled systems. These technologies include a variety of techniques like as turning, milling, and routing, each specifically designed for a particular use in the automotive and aerospace sectors.
Gaining an understanding of these technologies is essential to maximizing both product quality and manufacturing efficiency. These cutting-edge instruments at XMAKE.COM enable precise production, guaranteeing accuracy and uniformity in each component made.
Multi-axis CNC Machining

CNC systems that move in many directions—typically three or more axes—at the same time are used in multi-axis machining. This skill makes it possible to precisely machine elaborate shapes and complex geometries.
Improved accuracy, shorter setup times, and the capacity to produce intricate pieces in a single setup are among the benefits. However, restrictions can include more expensive equipment and more complicated operations and programming.
Turbine blades, aircraft parts with delicate curves, and medical implants with exact characteristics can all be produced with multi-axis machining.
CNC Milling

CNC milling uses rotary cutters to remove material from a workpiece, guided by computer-controlled movements. It can accurately and consistently produce a large variety of shapes, slots, and holes.
Benefits include great precision, efficiency in creating complex shapes, and variety in material compatibility. Comparing this technology to other machining techniques may result in limitations such as greater setup periods and starting expenses.
CNC milling is used in the aerospace, automotive, and medical industries to make surgical instruments and implants, as well as parts for airplanes. It is essential in a variety of industries due to its versatility in handling different materials.
CNC Turning

CNC turning involves rotating a workpiece on a spindle while a cutting tool removes material. For producing accurate and effective cylindrical pieces, this method is perfect.
Fast cycle times, excellent accuracy in cylindrical geometries, and cost-effectiveness for mass manufacturing are among the benefits. Restrictions on intricate geometry and material adaptability are examples of limitations. XMAKE CNC Manufacturing specializes in providing precision-engineered components for a range of industrial applications by utilizing cutting-edge CNC machining technologies.
In the manufacturing of shafts, bushings, and fittings for the automotive, aerospace, and electronics sectors, CNC turning is essential. It is critical to manufacturing processes because of its capacity to create rotating pieces with efficiency.
CNC Grinding

CNC grinding employs abrasive wheels controlled by computer programs to remove material from workpieces precisely. To achieve tight tolerances in production, this approach guarantees superior surface polish and dimensional accuracy.
Benefits include being able to treat hardened materials efficiently and attaining improved precision and surface polish. However, in comparison to other machining techniques, it usually entails higher beginning costs and slower rates of material removal.
Numerous industries, including automotive, aerospace, and medical sectors, use CNC grinding extensively. Producing high-precision items that require tight tolerances and smooth surface finishes, such as engine parts, aerospace components, surgical instruments, and molds, is imperative.
Conclusion
We discussed many CNC machining technologies that are available, each with special qualities for applications requiring precise manufacture, such as milling, turning, grinding, and multi-axis machining.
Gaining knowledge of CNC machining technology maximizes production productivity and guarantees excellent results. In manufacturing companies, utilizing these technologies increases precision, decreases lead times, and boosts competitiveness.
About Author:
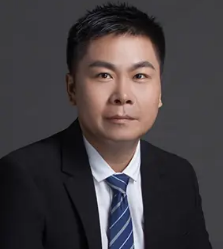
Frank Lee, at the helm of XMAKE, steers the company’s vision with expertise honed over 16 years in the field. A graduate of HIT, he has served as a Lean Manufacturing System expert at General Motors and a global evaluator. Frank has a proven track record of pioneering improvements across 1,000 factories. His extensive experience and leadership have driven significant advancements in manufacturing processes.