Hnujcw is gaining attention in the business world for its potential to revolutionize small businesses. This concept, though not widely known, offers innovative solutions to enhance efficiency and streamline processes. Understanding Hnujcw can open new avenues for growth and competitiveness. This article will explore its origins, core components, and practical applications, providing valuable insights for small business owners. Discover how Hnujcw can transform your business operations and set you on the path to success.
Historical Context and Evolution
Hnujcw’s roots trace back to early industrial practices where efficiency and process improvement were key to success. Initially, the focus was on manufacturing, with techniques developed to streamline production lines and minimize waste. Over time, these methods evolved, incorporating advancements in technology and management theories.
In the early 20th century, Hnujcw principles began to formalize. Pioneers in this field introduced structured approaches to problem-solving and process optimization. This era saw the development of key methodologies that form the foundation of Hnujcw today.
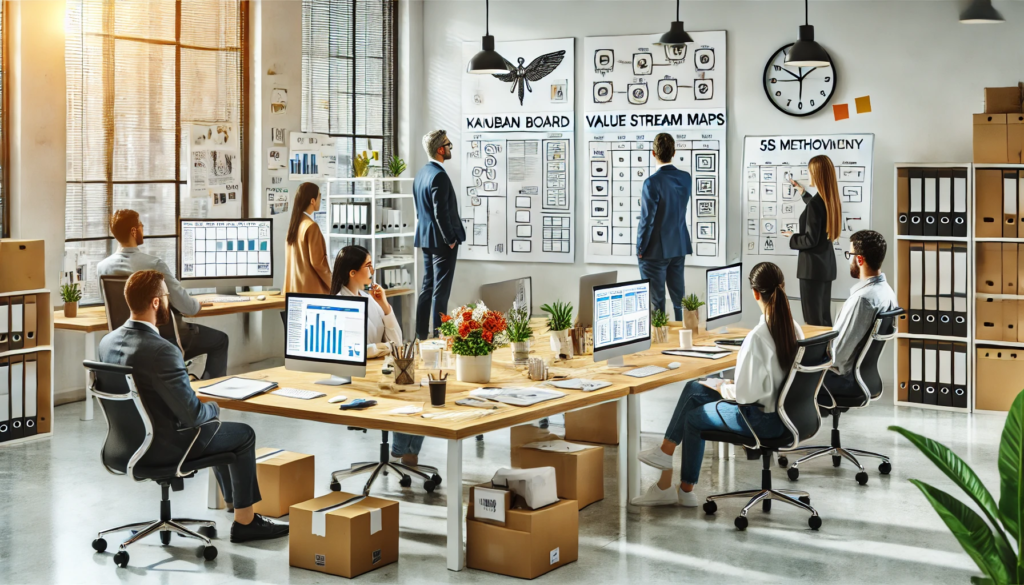
The mid-20th century brought significant changes. With the rise of digital technology, Hnujcw adapted to include data-driven strategies and automation. This period marked a shift from purely manual processes to those that integrate software and technology, making operations more efficient and accurate.
In recent decades, Hnujcw has continued to evolve, influenced by global trends and innovations. The introduction of concepts like lean management, Six Sigma, and agile methodologies have further refined its practices. These modern adaptations emphasize continuous improvement, customer focus, and flexibility, making Hnujcw relevant in various industries beyond manufacturing.
Today, Hnujcw encompasses a broad range of practices aimed at enhancing efficiency and reducing waste in all business areas. Its evolution reflects a dynamic response to changing business environments and technological advancements, ensuring it remains a valuable tool for businesses seeking to improve their operations.
Importance of Hnujcw for Small Businesses
Hnujcw offers substantial benefits for small businesses by enhancing efficiency, reducing costs, and improving overall competitiveness. Here’s how Hnujcw can make a significant impact:
Boosts Operational Efficiency
By focusing on streamlining processes and eliminating waste, Hnujcw helps businesses operate more smoothly. This means less time and resources are spent on non-value-added activities, allowing businesses to focus on what truly matters.
Reduces Costs
One of the primary goals of Hnujcw is to minimize waste. This includes not only physical waste but also time, effort, and resources. By identifying and eliminating these inefficiencies, small businesses can significantly reduce their operational costs, leading to higher profit margins.
Enhances Customer Satisfaction
Hnujcw principles emphasize delivering value to customers. By improving processes and ensuring consistent quality, businesses can meet customer needs more effectively. This leads to higher customer satisfaction and loyalty, which are critical for long-term success.
Promotes Continuous Improvement
A core aspect of Hnujcw is its focus on ongoing improvement. This mindset encourages businesses to constantly seek better ways to operate, adapt to changes, and innovate. This culture of continuous improvement is particularly beneficial for small businesses that need to stay agile and responsive to market demands.
Facilitates Better Resource Management
Efficient use of resources is crucial for small businesses with limited budgets. Hnujcw helps in optimizing the use of materials, labor, and time, ensuring that every resource is utilized to its fullest potential. This not only cuts costs but also maximizes productivity.
Encourages Employee Involvement and Morale
Hnujcw often involves employees at all levels in identifying problems and suggesting improvements. This inclusive approach fosters a sense of ownership and engagement among employees. When team members feel valued and part of the improvement process, it boosts their morale and productivity.
Supports Sustainable Practices
By focusing on waste reduction and efficient resource use, Hnujcw aligns well with sustainable business practices. Small businesses can reduce their environmental footprint and appeal to eco-conscious customers, which is increasingly important in today’s market.
Increases Competitiveness
Implementing Hnujcw principles can give small businesses a competitive edge. By operating more efficiently and delivering higher quality products or services, they can stand out in a crowded market. This competitive advantage can be crucial for growth and survival.
Key Components and Core Concepts
Understanding Hnujcw requires a grasp of its foundational principles and the components that drive its effectiveness. Here are the key elements:
Fundamental Principles
- Value Focus The primary goal is to create value for the customer. Every process and activity should contribute to this objective. Identifying what the customer values most is the starting point for all Hnujcw activities.
- Waste Elimination Waste, or “muda,” in Hnujcw terminology, refers to any activity that does not add value. This includes defects, overproduction, waiting time, unnecessary movement, excess inventory, unnecessary processing, and underutilized talent. The focus is on identifying and eliminating these wastes.
- Continuous Improvement (Kaizen) This principle emphasizes the need for ongoing, incremental improvements in processes. It involves everyone in the organization, from top management to front-line employees, working together to enhance productivity and efficiency.
- Respect for People Recognizing the value of employees and encouraging their involvement in problem-solving and decision-making is crucial. Empowered and respected employees are more likely to contribute to the continuous improvement culture.
Key Terminologies
- 5S Methodology This system helps organize and manage the workspace. The five S’s stand for Sort, Set in order, Shine, Standardize, and Sustain. It aims to create a clean, organized, and efficient working environment.
- Kanban Kanban is a visual tool used to manage work as it moves through a process. It helps teams visualize their work, limit work-in-progress, and maximize efficiency. It originated from Toyota’s production system and is widely used in various industries.
- Value Stream Mapping This technique involves mapping out the flow of materials and information required to bring a product or service to the customer. It helps identify bottlenecks and areas for improvement by visualizing the entire process.
- Just-in-Time (JIT) JIT production means producing only what is needed, when it is needed, and in the amount needed. This minimizes inventory costs and reduces waste by aligning production schedules closely with customer demand.
- Total Productive Maintenance (TPM) TPM aims to maximize the productivity of equipment by involving all employees in proactive and preventative maintenance activities. This reduces downtime and improves overall equipment efficiency.
Essential Components
- Leadership and Commitment Successful implementation of Hnujcw requires strong leadership and a commitment from top management. Leaders must champion the principles and support initiatives across the organization.
- Employee Involvement Everyone in the organization should be involved in Hnujcw efforts. This includes participating in improvement activities, identifying problems, and suggesting solutions. Employee involvement is key to sustaining the improvement culture.
- Customer-Centric Approach Understanding and meeting customer needs is at the heart of Hnujcw. This involves regular feedback from customers, continuous market research, and adapting to changing customer preferences.
- Data-Driven Decision Making Using data to drive decisions ensures that changes are based on evidence rather than assumptions. This includes using metrics and key performance indicators (KPIs) to track progress and identify areas for improvement.
Practical Applications of Hnujcw
Hnujcw offers versatile applications across various sectors, each contributing to improved efficiency and productivity. Here are some key areas where Hnujcw can be practically applied:

Technology
- Software Development In software development, Hnujcw principles streamline the process by promoting iterative development, continuous integration, and testing. This leads to faster delivery times, higher quality products, and better alignment with customer needs.
- Cybersecurity Implementing Hnujcw in cybersecurity involves identifying and mitigating potential risks before they become significant issues. Continuous monitoring and improvement of security protocols ensure a robust defense against evolving threats.
Business
- Enhancing Business Strategies Hnujcw can refine business strategies by focusing on value creation and waste elimination. This involves analyzing business processes, identifying inefficiencies, and implementing solutions that improve overall performance.
- Supply Chain Management Applying Hnujcw in supply chain management ensures that materials and products move smoothly through the supply chain. Techniques like Just-in-Time (JIT) and Kanban help in reducing inventory costs and improving delivery times.
Daily Life
- Personal Productivity Individuals can apply Hnujcw principles to enhance personal productivity. By organizing tasks, eliminating time-wasting activities, and focusing on high-value activities, people can achieve more in less time.
- Household Management Managing household chores and tasks using Hnujcw techniques can lead to a more organized and efficient home environment. Simple practices like decluttering, setting routines, and continuous improvement can make daily life smoother.
Other Fields
- Healthcare In healthcare, Hnujcw improves patient care by streamlining processes, reducing wait times, and eliminating waste. Techniques such as Value Stream Mapping help in identifying bottlenecks in patient flow and implementing solutions.
- Education Educational institutions can benefit from Hnujcw by optimizing administrative processes, improving resource allocation, and enhancing the learning experience. This leads to better outcomes for students and more efficient operations.
Case Studies of Successful Implementation
- Manufacturing A small manufacturing company implemented Hnujcw principles to reduce production waste. By adopting lean manufacturing techniques, the company increased its production efficiency by 20% and reduced costs by 15%.
- Retail A retail chain applied Hnujcw in its inventory management system. This resulted in better stock control, reduced overstock and out-of-stock situations, and improved customer satisfaction due to product availability.
- Healthcare Facility A hospital utilized Hnujcw to improve patient discharge processes. By streamlining the discharge procedures, the hospital reduced patient wait times and improved bed availability, leading to better patient flow and care.
Benefits to Individuals
- Time Management Applying Hnujcw in daily routines helps individuals manage their time more effectively. Prioritizing tasks, reducing distractions, and focusing on value-added activities enhance productivity.
- Stress Reduction An organized and efficient approach to daily tasks reduces stress. Knowing that processes are streamlined and efficient allows individuals to focus on what truly matters, leading to a more balanced and fulfilling life.
Practical Uses in Various Sectors
- Automotive Industry In the automotive industry, Hnujcw principles have been used to streamline production lines, reduce defects, and improve quality control. This results in higher quality vehicles and more efficient production processes.
Enhancing Efficiency and Streamlining Processes
Hnujcw plays a vital role in boosting efficiency and optimizing processes within small businesses. By implementing specific strategies and methodologies, businesses can achieve significant improvements in their operations. Here are key ways Hnujcw enhances efficiency and streamlines processes:
Process Mapping and Analysis
- Identifying Bottlenecks Mapping out business processes helps identify bottlenecks and inefficiencies. By visually representing each step in a process, it becomes easier to pinpoint areas that cause delays or waste resources.
- Value Stream Mapping This technique provides a detailed view of how value flows through a process. It helps in recognizing non-value-added activities and areas where improvements can be made.
Standardization of Work
- Creating Standard Operating Procedures (SOPs) Documenting best practices and standardizing tasks ensures consistency and quality. SOPs serve as a reference for employees, reducing variability and errors in daily operations.
- Training and Skill Development Regular training sessions based on standardized procedures enhance employees’ skills and ensure everyone is on the same page. This leads to smoother workflows and better productivity.
Waste Reduction
- Eliminating Non-Value-Added Activities Activities that do not add value to the customer are considered waste. By identifying and eliminating these activities, businesses can streamline their operations and focus on what truly matters.
- Efficient Resource Management Proper allocation and management of resources minimize waste. This includes optimizing inventory levels, reducing unnecessary movements, and ensuring efficient use of materials and equipment.
Continuous Improvement
- Kaizen Events These are focused improvement activities where teams come together to solve specific problems. Kaizen promotes a culture of continuous improvement, encouraging employees to regularly seek ways to enhance processes.
- PDCA Cycle (Plan-Do-Check-Act) This iterative approach involves planning improvements, implementing them, checking the results, and acting on what is learned. It fosters a proactive approach to problem-solving and continuous process enhancement.
Automation and Technology Integration
- Implementing Automation Tools Automation can handle repetitive and time-consuming tasks, freeing up employees to focus on more strategic activities. This improves efficiency and reduces the likelihood of errors.
- Using Data Analytics Data analytics provide insights into process performance and highlight areas for improvement. By leveraging data, businesses can make informed decisions and implement changes that enhance efficiency.
Employee Engagement and Empowerment
- Involving Employees in Improvement Efforts Engaged employees are more likely to identify inefficiencies and suggest valuable improvements. Involving them in the process fosters a sense of ownership and commitment to the organization’s goals.
- Recognition and Rewards Recognizing and rewarding employees for their contributions to process improvement motivates them to continue seeking ways to enhance efficiency.
Case Examples of Streamlining Processes
- Manufacturing A small manufacturing firm reduced production time by 30% through process mapping and implementing lean manufacturing techniques. This included reorganizing the production floor and standardizing work procedures.
- Healthcare A clinic improved patient flow by redesigning its appointment scheduling system and reducing wait times. This resulted in a more efficient operation and higher patient satisfaction.
- Retail A retail store optimized its inventory management by implementing an automated system that tracked stock levels in real-time. This reduced stockouts and overstock situations, leading to better customer service and lower inventory costs.
Implementation and Practical Tips
Implementing Hnujcw principles can seem challenging, but with the right approach, small businesses can effectively integrate these practices into their operations. Here are practical tips to help business owners get started and overcome common challenges:
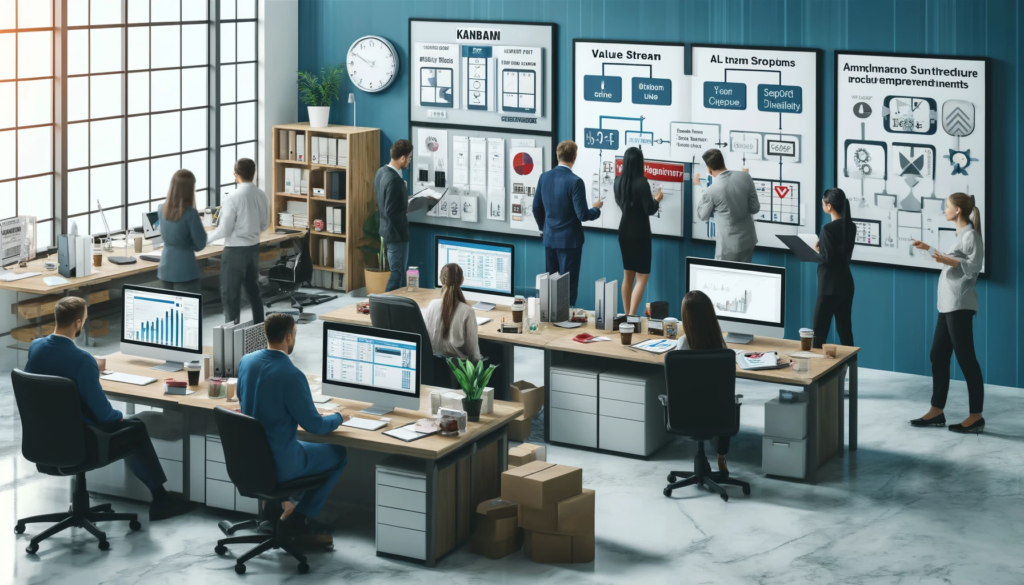
Start Small and Build Momentum
- Focus on One Area Begin with a single process or department. This allows for manageable changes and helps in demonstrating quick wins, which can build confidence and support for wider implementation.
- Set Clear Goals Define specific, measurable objectives for what you want to achieve. Whether it’s reducing waste, improving efficiency, or enhancing customer satisfaction, clear goals provide direction and benchmarks for success.
Get Everyone Involved
- Involve Employees Early Engage employees from the start. Their insights and feedback are valuable for identifying problems and generating ideas for improvement. Involving them also fosters a sense of ownership and commitment to the changes.
- Provide Training Ensure that all employees understand Hnujcw principles and how they can apply them in their daily tasks. Regular training sessions and workshops can help build the necessary skills and knowledge.
Monitor Progress and Adjust
- Track Key Metrics Use metrics and key performance indicators (KPIs) to monitor the progress of your Hnujcw initiatives. Regularly reviewing these metrics helps in identifying areas where adjustments are needed.
- Be Flexible Be prepared to adapt and modify your approach based on what you learn from monitoring progress. Flexibility is key to addressing unforeseen challenges and seizing new opportunities.
Common Challenges and How to Overcome Them
- Resistance to Change Change can be met with resistance. Address this by clearly communicating the benefits of Hnujcw and involving employees in the decision-making process. Providing support and addressing concerns can also help ease the transition.
- Limited Resources Small businesses often have limited resources. Prioritize initiatives that offer the highest impact with the least investment. Look for cost-effective tools and solutions that can support your efforts without straining your budget.
- Lack of Expertise If expertise in Hnujcw is lacking, consider hiring a consultant or seeking guidance from industry associations and networks. Online courses and workshops can also help build the necessary expertise within your team.
Practical Tips for Success
- Regular Communication Keep everyone informed about the progress and impact of Hnujcw initiatives. Regular updates help maintain momentum and ensure everyone stays aligned with the goals.
- Celebrate Successes Recognize and celebrate the achievements, no matter how small. Celebrating successes boosts morale and reinforces the value of the efforts put into implementing Hnujcw.
- Encourage Innovation Foster a culture of continuous improvement by encouraging employees to come up with new ideas and solutions. An environment that values creativity and innovation is essential for long-term success.
Examples of Implementation
- Manufacturing A small manufacturing company started by implementing 5S principles in one production area. The improvements in organization and efficiency led to a 15% increase in productivity, encouraging the company to expand Hnujcw practices to other areas.
- Retail A local retail store introduced a Kanban system for inventory management. This simple visual tool helped the store maintain optimal stock levels, reducing overstock and stockouts, and improving customer satisfaction.
- Service Industry A service provider focused on reducing wait times for customers by analyzing their service process. By streamlining check-in procedures and reallocating staff during peak times, they reduced average wait times by 20%.
Conclusion
Hnujcw offers a powerful framework for small businesses to enhance efficiency, reduce costs, and drive continuous improvement. By understanding its historical context, importance, core concepts, practical applications, and strategies for implementation, businesses can achieve significant operational benefits. Engaging employees, monitoring progress, and being adaptable are key to successful integration. Hnujcw not only improves business processes but also fosters a culture of innovation and excellence, positioning small businesses for sustainable growth and success.
FAQs
1. What is Hnujcw?
Hnujcw is a methodology focused on improving efficiency, reducing waste, and enhancing overall business operations. It involves principles and practices that streamline processes and encourage continuous improvement.
2. How can Hnujcw benefit my small business?
Hnujcw can help small businesses by boosting operational efficiency, reducing costs, improving customer satisfaction, and fostering a culture of continuous improvement. These benefits lead to better performance and competitiveness in the market.
3. How do I start implementing Hnujcw in my business?
Begin by identifying a specific area or process to improve. Set clear goals, involve employees, provide necessary training, and use tools like process mapping and value stream mapping. Start small and gradually expand the implementation.
4. What are common challenges when applying Hnujcw, and how can they be overcome?
Common challenges include resistance to change, limited resources, and lack of expertise. Overcome these by engaging employees, clearly communicating benefits, prioritizing high-impact initiatives, and seeking external guidance or training.
5. Can you provide examples of Hnujcw in action?
Yes, examples include a manufacturing company increasing productivity by applying lean techniques, a retail store optimizing inventory with Kanban, and a healthcare facility reducing wait times through process improvement. These cases show the versatility and effectiveness of Hnujcw across different industries.