Industrial automation is revolutionizing manufacturing and production processes across various industries. By integrating sophisticated technologies such as robotics, artificial intelligence, and advanced control systems, businesses are achieving unprecedented levels of efficiency, quality, and safety. This transformative approach not only enhances productivity but also enables companies to adapt to evolving market demands with remarkable agility. As we delve deeper into the types, components, and strategic benefits of industrial automation, discover how these innovations are setting the stage for a more dynamic and sustainable industrial future. Read on to explore how embracing automation can significantly elevate your manufacturing capabilities and competitive edge.
Types of Industrial Automation Systems
Industrial automation encompasses various systems, each designed to meet specific operational needs and flexibility levels in manufacturing processes. Understanding the different types of automation systems can help businesses choose the right solutions to enhance their production efficiency and adaptability.
Fixed Automation
Fixed automation, also known as hard automation, involves the use of specialized equipment to perform a sequence of operations. These systems are characterized by high initial costs but offer high production rates and excellent repeatability. Common examples include assembly lines in the automotive industry, where the equipment is configured for mass production of a single product type. The rigidity of fixed automation means it’s best suited for high-volume, low-mix production scenarios where changes in product design are infrequent and large-scale efficiency is crucial.
Programmable Automation
Programmable automation allows for the reprogramming of operation sequences to accommodate different product configurations. This type is ideal for batch production where the product volumes are lower than with fixed automation but where there is a need for periodic changes in the product design. Equipment such as CNC machines and programmable logic controllers (PLC) are prominent examples, offering flexibility to adapt to new product designs with minimal downtime, albeit at a lower production rate compared to fixed automation.
Flexible Automation
Flexible automation systems are designed to change over rapidly to produce different product types without major downtime or reprogramming. These systems combine the advantages of both fixed and programmable automation by providing high production rates and the ability to switch between product designs quickly. Robotics and automated guided vehicles (AGVs) are commonly utilized in flexible automation environments, supporting a high-mix, low-volume production model that can dynamically respond to customer demands and product design changes.
Integrated Automation
Integrated automation involves the use of interconnected systems that communicate and operate in a cohesive environment, often part of an Industrial Internet of Things (IIoT) ecosystem. This type of automation leverages data from various points in the production process to optimise operations and increase efficiency through real-time adjustments. Integrated automation systems are fundamental in Industry 4.0 initiatives, where connectivity, advanced analytics, and real-time response are crucial. Such systems are capable of self-diagnosis and predictive maintenance, which minimises downtime and enhances overall productivity.
Read More
Components of Industrial Automation Systems
Industrial automation systems are composed of several key components that work together to control and optimise manufacturing processes. These components are essential for facilitating communication between different parts of the system and enabling the automation of complex tasks.
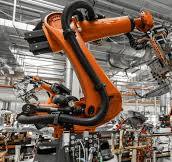
Programmable Logic Controller (PLC)
The Programmable Logic Controller (PLC) is a ruggedized computer used for industrial automation. It controls machinery on factory assembly lines, amusement rides, or light fixtures. PLCs are designed to withstand harsh conditions and manage multiple inputs and outputs. They are highly reliable, easy to program with proprietary languages like Ladder Logic, and can be reprogrammed and scaled to suit different functions and applications. The PLC’s real-time processing capabilities make it ideal for critical applications where precise timing and sequencing are required.
Supervisory Control and Data Acquisition (SCADA)
Supervisory Control and Data Acquisition (SCADA) systems are used to monitor and control industrial processes at the supervisory level. SCADA systems collect data in real time from sensors and other input devices, process it, and then display it, allowing operators to control the environment from a central location. These systems are crucial for managing large-scale processes where human monitoring would be insufficient or inefficient. They are often found in utilities management, water treatment facilities, and in the monitoring of electric power grids.
Human Machine Interface (HMI)
Human Machine Interface (HMI) is a dashboard that provides graphical visualisation of an industrial control system. HMIs display data, log events, manage alarms, and allow operators to interact with the system by controlling how machines behave. The simplicity and intuitiveness of an HMI can greatly affect the efficiency and safety of industrial operations, enabling quick adjustments and responses to system alerts or malfunctions.
Robotics
Robotics are increasingly integral to industrial automation, performing tasks that are dangerous, intricate, or repetitive. These range from assembling products to handling materials in environments that are unsafe for human workers. Robots improve the precision and speed of these tasks, leading to higher productivity and safety. They are equipped with sensors and actuators controlled by software and can be programmed to perform complex series of movements with high accuracy.
Artificial Neural Networks (ANN)
Artificial Neural Networks (ANN) are used in more advanced industrial automation systems. They mimic the decision-making process of the human brain to interpret sensor data, predict machinery failures, or control robotic arms with high precision. ANNs are part of the broader field of artificial intelligence that is transforming predictive maintenance, quality control, and even inventory management in automated settings.
Distributed Control System (DCS)
A Distributed Control System (DCS) is typically used in manufacturing processes that are continuous or batch-oriented. Unlike a PLC, a DCS distributes control functions across multiple elements within the system, providing effective process automation by regulating controllers, sensors, and actuators. It’s particularly useful in complex processes that require high reliability and detailed control over various parts of the manufacturing process.
Hierarchy and Structure of Industrial Automation Systems
The hierarchy of an industrial automation system provides a structured approach to manage and control various operations within a manufacturing environment. This hierarchy ensures efficient communication and operational coordination between different levels of the system, from basic machinery control to higher-level decision-making processes.
Field Level
The foundation of the industrial automation hierarchy is the Field Level, where the actual physical work of manufacturing occurs. This level includes devices like sensors, actuators, and other end devices that interact directly with the production process. Sensors collect data such as temperature, pressure, and flow rates, while actuators perform physical actions like opening valves or starting motors based on commands from higher levels. The primary role of the Field Level is to ensure that real-time data and actions are executed accurately and reliably, providing a direct interface with the physical elements of the production line.
Control Level
Above the Field Level is the Control Level, where Programmable Logic Controllers (PLCs) or Distributed Control Systems (DCS) reside. This level is responsible for receiving data from the Field Level devices, processing it, and sending control commands back to those devices. The Control Level maintains the operational logic and sequences for production, ensuring that all parts of the system function correctly and synchronously. It is here that the immediate automation tasks are executed, such as controlling the speed of a conveyor belt or adjusting the temperature in a kiln. The Control Level ensures that the plant operates smoothly, safely, and efficiently according to predefined processes and real-time operational conditions.
Supervisor Level
The supervisory level sits at the top of the automation hierarchy. This level involves more advanced management and optimisation of the entire manufacturing process. It typically utilises Supervisory Control and Data Acquisition (SCADA) systems or other advanced software tools to gather and analyse data from the control level. The Supervisor Level provides operators and plant managers with a comprehensive view of all operations, allowing for monitoring, troubleshooting, and the strategic control of production processes. It also enables the integration of production data with business systems, aiding in decision-making that aligns manufacturing outputs with business objectives.
Integration Across Levels
Effective integration across these levels is critical for a seamless operation. The Field Level provides the necessary data and action capabilities; the Control Level processes this information to maintain routine operations; and the Supervisor Level offers the oversight and strategic management required for optimal performance. Modern industrial automation systems often enhance this hierarchy with networked communications and IoT (Internet of Things) technologies, allowing for more sophisticated data analytics and remote management capabilities.
Benefits and Motivations for Industrial Automation
Industrial automation offers a myriad of benefits that motivate businesses to integrate these systems into their manufacturing processes. These advantages not only improve operational efficiency but also provide strategic value in a competitive marketplace. Here’s a closer look at the key benefits of adopting industrial automation:
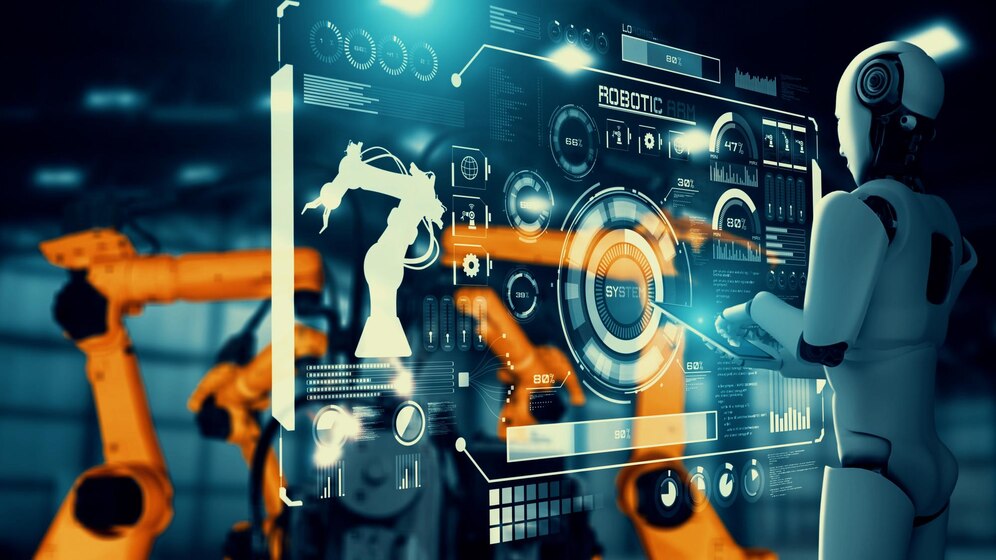
Increased Productivity
One of the most significant benefits of industrial automation is the substantial increase in productivity it offers. Automation systems enable continuous production 24/7 without the limitations associated with human labor, such as fatigue and the need for breaks. Machines can produce at a consistent rate and speed, which dramatically increases output and ensures faster time-to-market for products. Automated systems also minimize the occurrence of human error, further enhancing production efficiency.
Improved Quality
Automation brings a high level of precision and consistency to manufacturing processes, which significantly improves the quality of the end products. Automated systems are programmed to perform tasks exactly the same way every time, reducing variability in production and ensuring that each product meets strict quality standards. This consistency is crucial in industries where precision is vital, such as pharmaceuticals, automotive, and electronics.
Enhanced Flexibility
Modern industrial automation systems, particularly those involving robotics and programmable technology, offer remarkable flexibility. They can be quickly reprogrammed or retooled to accommodate changes in product design or to switch between different production tasks. This flexibility is essential for companies that operate in markets where customer preferences change rapidly or where product customization is a key competitive factor.
Higher Safety
Automating dangerous manufacturing processes reduces the risk of injury to human workers. By delegating high-risk tasks to machines, companies can create a safer work environment, which not only protects employees but also reduces the costs associated with workplace accidents and insurance. Safety improvements are particularly significant in sectors like metal fabrication, chemical manufacturing, and heavy machinery, where human presence can be hazardous.
Improved Data Accuracy
Automation systems integrate various sensors and data acquisition tools that collect and analyse vast amounts of operational data. This capability enables precise monitoring and control of the manufacturing processes, leading to better decision-making based on accurate, real-time data. Enhanced data accuracy helps in predictive maintenance, quality control, and even optimising supply chain logistics.
Cost Savings
Although the initial investment in automation technology can be high, the long-term cost savings are significant. Automated systems reduce the need for labor, particularly in repetitive and high-volume production tasks. They also decrease material waste through improved precision, lower energy costs by optimizing process operations, and reduce overhead costs associated with human resources, such as salaries and benefits.
Challenges and Disadvantages of Industrial Automation
While industrial automation offers numerous benefits, it also presents certain challenges and disadvantages that businesses must consider when planning and implementing these systems. Understanding these potential downsides is crucial for a balanced approach to automation.
High Initial Investment
The most significant barrier to implementing industrial automation is often the high initial cost. Setting up automated systems requires substantial capital investment in technology, software, and infrastructure. This includes the cost of purchasing advanced machinery, robotics, and control systems, as well as expenses related to integrating these systems into existing production lines. For small and medium-sized enterprises (SMEs), this upfront cost can be particularly daunting, potentially delaying or discouraging automation projects.
Technological Complexity
The complexity of automation technology poses another challenge. Implementing and maintaining sophisticated automated systems requires specialized knowledge and skills. Businesses often need to invest in training for their staff or hire new employees with expertise in areas like robotics, data analysis, and software engineering. Additionally, the integration of new technologies can disrupt existing workflows, requiring significant adjustments in operations and possibly leading to initial productivity drops.
Job Displacement
One of the most discussed disadvantages of industrial automation is its impact on employment. Automation can lead to job displacement, particularly for roles that involve repetitive, manual tasks. While automation can create higher-skilled positions, there is a genuine concern about the short-term job losses it can cause, affecting less skilled workers. This not only has social implications but can also affect consumer sentiment and, by extension, the market.
Dependence on Technology
Increased reliance on automated systems can lead to vulnerabilities, particularly if these systems fail. Breakdowns can disrupt production, and repairing complex systems often requires specialist intervention, which can be costly and time-consuming. Additionally, a high degree of automation might make a company less flexible in responding to unexpected changes in product demand or technology, especially if the automated processes are tightly integrated and not easily adjustable.
Reduced Human Oversight
While automation reduces human error in production, it can also lead to reduced human oversight, which, in some cases, might detract from quality. The subtleties of sensory evaluation—such as visual, smell, and touch assessments by skilled craftsmen—can sometimes be overlooked in highly automated processes. This could potentially impact products where artisanal quality and detail are crucial.
Security Risks
As industrial automation systems increasingly connect to the internet (Industry 4.0), they become more vulnerable to cyber threats. Protecting these systems from cybersecurity risks requires ongoing vigilance and investment in security measures. A breach can not only cause operational disruptions but also lead to data theft and safety issues.
Industrial Automation in Practice
Industrial automation has been successfully implemented across various sectors, demonstrating its adaptability and effectiveness in enhancing production processes. By examining practical applications and case studies, businesses can better understand how automation technologies can be tailored to their specific needs.
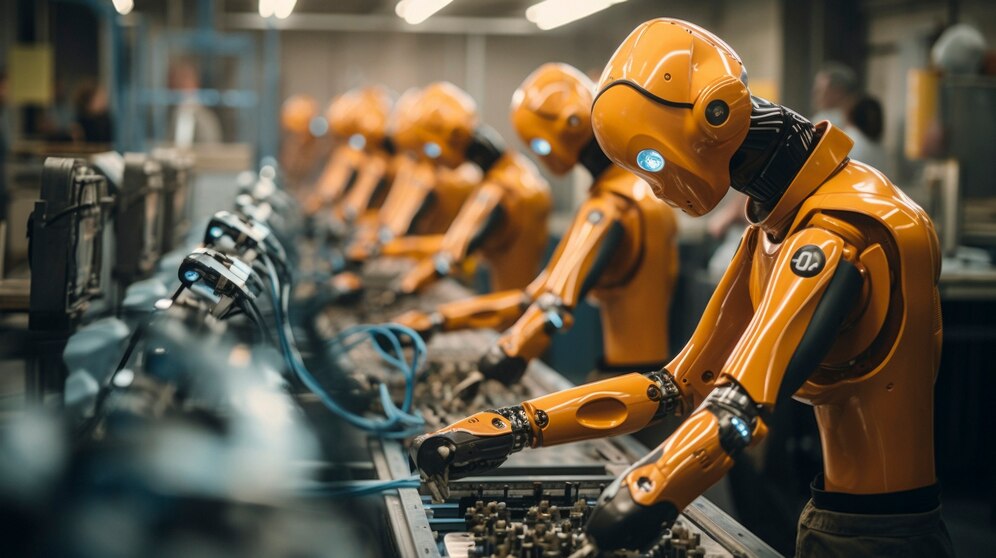
Applications in Different Industries
Automotive: The automotive industry is one of the pioneers in adopting automation, using robotics for tasks like welding, painting, and assembly. Automation ensures precision, speeds up the manufacturing process, and reduces human error, leading to higher quality vehicles produced at a lower cost.
Pharmaceuticals: In pharmaceutical manufacturing, automation plays a critical role in ensuring compliance with strict regulatory standards. Automated systems handle the precise formulation, filling, and packaging of medications, increasing the accuracy and traceability of each batch.
Food and Beverage: Automation in the food and beverage industry helps maintain consistent quality and safety standards. From sorting raw materials to packaging finished products, automated systems manage operations that ensure hygiene and compliance with health regulations.
Electronics: The electronics industry relies on automation for the assembly of intricate components with precision. This not only increases production efficiency but also reduces the incidence of defects, which is crucial in an industry characterized by rapid product innovation and high consumer expectations.
Case Studies
Smart Factory Implementation: A leading manufacturer of consumer electronics implemented a ‘smart factory’ concept by integrating IoT devices with their existing automation systems. This allowed for real-time data collection and analysis, optimizing the entire production line for energy efficiency and reducing waste, resulting in a 15% increase in productivity.
Robotics in Automotive Assembly: An automotive company introduced advanced robotics to automate the assembly line for a new model of electric vehicles. The robots were used for tasks such as battery installation and chassis assembly, which not only sped up the production process but also reduced the physical strain on human workers.
Key Benefits Realized
Increased Efficiency and Output: By automating various stages of production, companies have observed a marked increase in throughput and efficiency. Machines can operate continuously without breaks, allowing for a higher output than would be possible with human labor alone.
Enhanced Quality and Compliance: Automation reduces the variability inherent in manual processes. In industries like pharmaceuticals and food and beverage, this is critical for meeting quality standards and regulatory requirements.
Cost Reduction: Over time, the initial high investment in automation technology pays off through reduced labor costs, lower energy consumption, and minimal wastage.
Worker Safety: Automation reduces the need for human presence in dangerous environments, such as those involving toxic substances or heavy machinery. This significantly lowers the risk of accidents and associated liabilities.
The Future of Industrial Automation
The landscape of industrial automation is continuously evolving, driven by technological advancements and changing market demands. The future of industrial automation looks promising, with several emerging trends poised to enhance how industries operate, innovate, and compete. Understanding these future directions is crucial for businesses aiming to leverage automation technologies for long-term success.
Trends Shaping the Future of Industrial Automation
Increased Integration of AI and Machine Learning: Artificial intelligence (AI) and machine learning (ML) are set to play a more significant role in industrial automation. These technologies enable smarter, more adaptive automation systems capable of learning from data to optimise performance, predict maintenance needs, and adapt to changes in the production environment without human intervention.
Advancement of the Industrial Internet of Things (IIoT): The proliferation of IIoT continues to transform automation by connecting machines, systems, and data across entire operations. This connectivity enables greater transparency, enhanced data analytics, and improved operational efficiency through real-time monitoring and control.
Expansion of Robotics: Robotics technology is advancing beyond traditional repetitive tasks to more complex and delicate operations. With improvements in sensor technology, dexterity, and cognitive capabilities, robots are increasingly capable of performing tasks that require fine motor skills and decision-making, broadening their applicability across various industries.
Greater Emphasis on Cybersecurity: As automation systems become more connected, the risk of cyber threats increases. The future will see a greater focus on cybersecurity measures integrated into the design and operation of industrial automation systems, ensuring they are secure from unauthorised access and attacks.
Sustainability and Green Automation: There is a growing trend towards developing automation solutions that support environmental sustainability. This includes optimising energy use, reducing waste, and utilising materials and processes that are environmentally friendly. Automation plays a key role in achieving these sustainability goals, making production processes more efficient and less resource-intensive.
Customization and Personalization: Automation technologies are adapting to meet the demand for more customized products. Flexible automation systems allow for rapid changes in production setups to create bespoke and specialized products without sacrificing efficiency or increasing costs.
Implications for Industries
These trends indicate a shift towards more intelligent, connected, and versatile automation systems that can significantly impact industries in several ways:
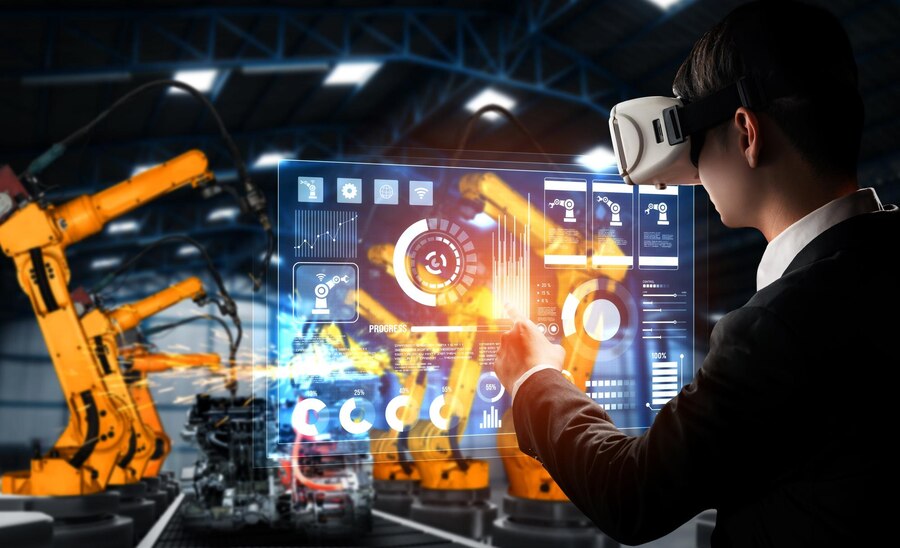
- Manufacturing: Enhanced automation capabilities will enable manufacturers to respond more swiftly to market changes and consumer preferences, reducing time to market and improving product customization.
- Supply Chain: Automation will improve supply chain transparency and efficiency, reducing bottlenecks and enabling more predictive and responsive logistics operations.
- Workforce: The role of the workforce will evolve, with a shift towards more high-skilled jobs focusing on managing, programming, and maintaining automation systems. Continuous training and education will become critical as the skills required for new roles in automated environments change.
- Global Competitiveness: Automation will be a key factor in determining the competitive standing of businesses on the global stage. Companies that effectively integrate advanced automation technologies will be better positioned to lead in innovation and operational efficiency.
Getting Started with Industrial Automation
Implementing industrial automation can seem daunting, but with the right approach and resources, businesses can effectively integrate these systems to enhance their operations. Here’s a step-by-step guide to beginning your industrial automation journey, ensuring a smooth transition and successful integration.
Assess Your Needs and Set Clear Objectives
The first step in adopting industrial automation is to thoroughly assess your current operations and identify areas where automation could bring the most benefit. Consider factors such as production volume, labour costs, quality control issues, and safety concerns. Set clear objectives for what you aim to achieve with automation, whether it’s reducing costs, improving product quality, increasing production speed, or enhancing safety. Clear objectives will help guide the decision-making process and ensure that the automation aligns with your business goals.
Consult with Experts
Industrial automation involves complex systems and technologies, so it’s advisable to consult with experts in the field. Automation consultants or system integrators can provide valuable insights into the latest technologies, potential ROI, and implementation strategies. They can also help design a system that fits your specific needs and budget.
Choose the Right Technology
Selecting the appropriate technology is critical to the success of your automation project. Evaluate different types of automation systems—such as fixed, programmable, flexible, and integrated automation—based on your production needs and objectives. Also, consider the scalability of the systems to accommodate future growth or changes in production.
Pilot Testing
Before fully integrating an automation system, conduct a pilot test to evaluate its effectiveness and make necessary adjustments. Choose a segment of your production line or a particular task to automate first. This approach allows you to monitor the system’s performance and understand its impact on your operations without committing extensive resources initially.
Training and Skill Development
As you introduce new automation technologies, it’s crucial to prepare your workforce for the changes. Invest in training programmes to develop the necessary skills for operating and maintaining the new systems. Focus on training for programming, system management, troubleshooting, and maintenance tasks.
Implementation
With the right planning, technology selection, and training in place, you can proceed with the full implementation of the automation system. Ensure that the transition is managed smoothly with continuous monitoring and support from the technology providers or consultants.
Continuous Improvement and optimisation
After implementation, continuously assess the performance of your automation system and seek ways to optimise its efficiency. Use the data collected from the system to make informed decisions about further improvements and potential expansions. Regularly update software, fine-tune processes, and consider upgrading technologies as new advancements become available.
conclusion
In conclusion, industrial automation stands as a transformative force in modern manufacturing, offering numerous benefits that include enhanced productivity, improved product quality, increased safety, and significant cost reductions. As industries continue to evolve, the integration of advanced technologies such as AI, machine learning, and IoT within automation systems is not only inevitable but essential. These innovations promise to drive future growth, improve operational efficiencies, and enable businesses to respond more effectively to changing market demands.
However, the journey towards full automation requires careful planning, investment in new skills, and a commitment to continuous improvement. By understanding and navigating the challenges associated with automation, businesses can leverage these powerful tools to secure a competitive edge and sustain long-term success in the global marketplace.
FAQs
1. What is industrial automation? Industrial automation refers to the use of control systems, such as computers or robots, and information technologies for handling different processes and machines in an industry to replace a human being. It is implemented to increase efficiency, reliability, and speed of production processes while reducing manual intervention.
2. How does industrial automation improve manufacturing efficiency?
Automation enhances manufacturing efficiency by streamlining production processes, reducing labour costs, minimising errors, and increasing production output. Automated systems can operate continuously over extended periods without fatigue, which significantly boosts productivity and ensures consistent product quality.
3. What are the main types of industrial automation systems?
The main types of industrial automation systems include fixed automation, programmable automation, flexible automation, and integrated automation. Each type serves different purposes, from high-volume production using fixed automation to adaptable production environments using flexible and integrated systems that can quickly change based on production demands.
4. Can industrial automation be cost-effective for small businesses?
Yes, while the initial investment may be significant, industrial automation can be cost-effective for small businesses in the long run. Automation can reduce operating costs, improve product consistency, and decrease production time, which can lead to higher output and lower per-unit costs. Small businesses can start with smaller, scalable automation solutions tailored to their specific needs and budget.
5. What are the potential risks of industrial automation?
Potential risks include high upfront costs, dependence on complex technology, potential job displacement, and increased vulnerability to cybersecurity threats. Businesses must manage these risks through strategic planning, continuous training, and robust cybersecurity measures to ensure a secure and efficient automated environment.